Rice AIAA: Student Unmanned Aerial Systems Team
Our team of sophomores and freshmen won the Best Underclassman Design Project Award at the Rice University Engineering Design Showcase.
In 2022, I co-founded the Rice American Institute of Aeronautics and Astronautics chapter with the mission to promote interest and education in the aerospace industry.
As the structures lead on our chapter's SUAS team, I designed and manufactured the structural components of the aircraft such as the fuselage, nosecone, camera gimbal, fairing, and the integration of the wing, tail, and elevator with the rest of the aircraft.
(See the Design in SolidWorks section)
Our Award-Winning Engineering Design Showcase Poster
Competition Requirements and Initial Design Matrices:
Brief Competition Overview:
Construct an aircraft to autonomously fly mission waypoints and safely drop between 1-5 payloads within 15 feet of specified ground targets. Each aircraft is given payloads marked with a unique shape and color and must find the corresponding ground target with a vision system.
Competition Requirements:
Autonomously fly above 75 feet above ground level during the mission and stay within a defined flight boundary
Fly at least 12 miles in a single flight
Fly waypoints with a max error of 25 feet
Be able to turn with a radius of 150 feet
Have an angle of climb and descent of at least 20 degrees
Teams must safely deliver a 16oz water bottle in a payload enclosure weighing less than 5lbs
Initial Design Matrices:
To begin designing our aircraft, our team needed to determine the type of aircraft to make and the features of this aircraft considering the competition requirements and our own requirements (like cost, repairability, ease of construction, and more). We made these decisions with the design matrices in the slideshow below:
Bold indicates which design option we choose.





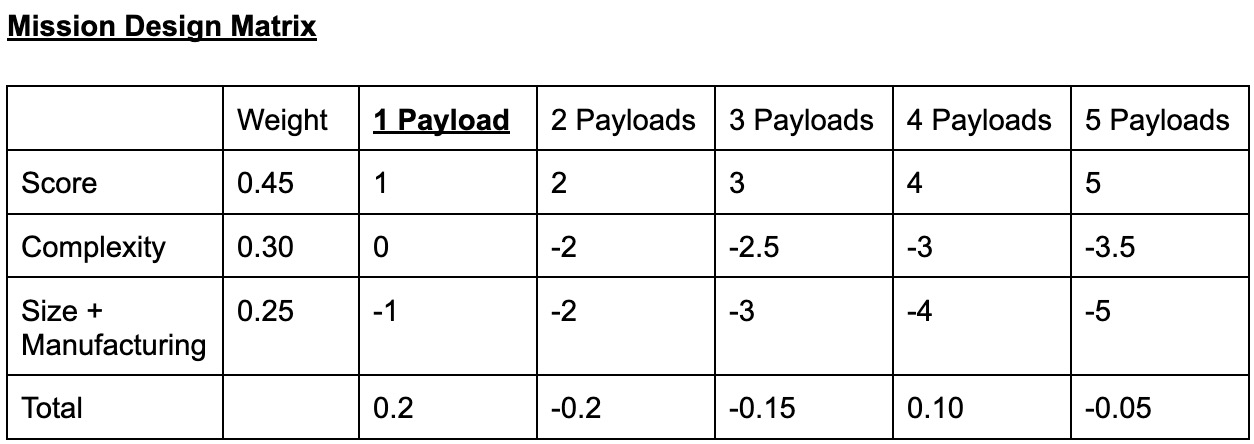

Our biggest decision was choosing between a multi-rotor (typical drone) or fixed-wing aircraft. We ended up choosing a fixed-wing aircraft since the competition required our aircraft to fly long distances quickly and efficiently. Initially, we were also considering a VTOL aircraft but we ruled this option out due to its complexity and our lack of relevant experience.
Another big decision was choosing between a composite tube fuselage or a wooden box fuselage. We ended up choosing to make our fuselage from a composite tube because it is more impact resistant (we expected to crash at some point) and because we can purchase it off the shelf instead of making it ourselves.
Design in SolidWorks:
As Structures Lead, I was responsible for the design of the fuselage shell, fuselage interiors, wing attachment coupler, nose cone, fairings, payload drop mechanism, and gimbal. My teammates designed the wings, tail, and electronics.
Very brief overview of what I designed:
These images to the right show how we thought about designing our fixed-wing aircraft. A tube-shaped fuselage design presented many benefits and challenges. The greatest benefits were having a strong and prebuilt structure to use and the greatest challenges were connecting/integrating the rest of the aircraft to a tube shape. We chose to uses fiberglass as our tube material for its impact resistance and its radio transparency. I sized our tube based off of the size of our batteries (which were our largest internal components) (the batteries sizing was determined by our motors and electronics).
With the size of our tube, I started designing the fuselage interiors. We used disk-shaped bulkheads with radial holes for mounting to provide interior structure and to support the removeable electronics sled. These bulkheads also had a round hole in the top to mount our tail on a carbon fiber tube.
Next, I designed our wing attachment method. Our wing fits into a cutout on the top of the fuselage and a carbon fiber tube inside the wing gets clamped to another carbon fiber tube inside the fuselage (see more images below).
I designed our nose cone to be aerodynamic, 3D printed (for easy manufacturing), have a cutout for a camera dome, and to be easily removable for access to the batteries. I also designed the highly compact two-axis camera gimbal which stabilized our 64-megapixel camera for sharp ground images.
Next, I designed the payload drop mechanism. We decided to use an externally mounted payload to save space inside the fuselage and simplify our design (no need for opening doors). We used a servo inside the fuselage to rotate a peg and release our payload. The payload was placed directly beneath the center of gravity.
Lastly, I designed a couple fairings to improve the aerodynamics above our wing and behind our fuselage.




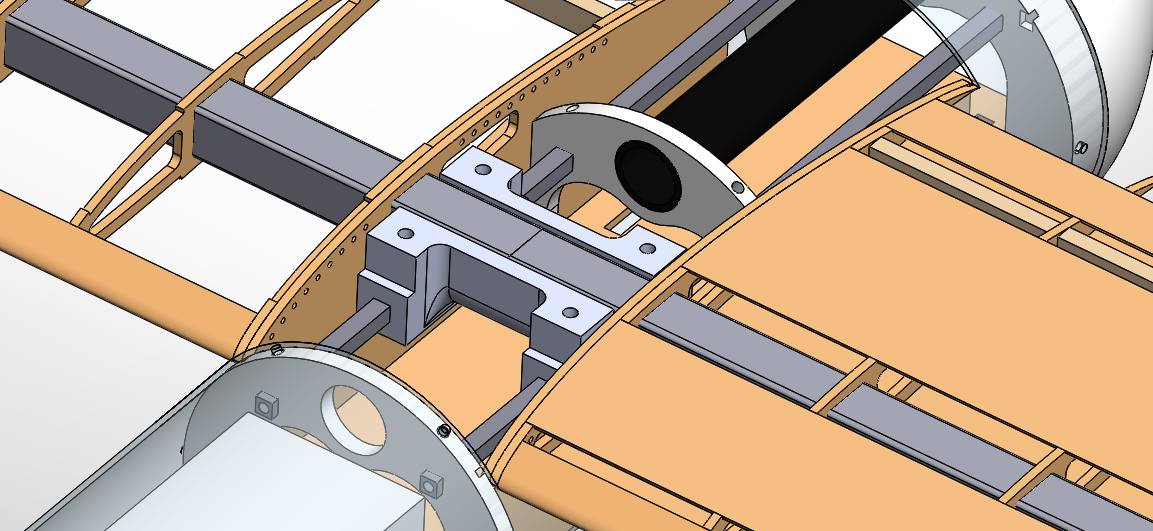

Manufacturing:
Manufacturing our plane was a ton of fun. We ran into very few manufacturing problems as our CAD model was very detailed so we knew exactly how to put it together. Manufacturing took significantly longer than expected and we were only left with two days left of the school year to flight test the plane. Here are a bunch of images from our build (I'm our only photographer):
First Test Flight:
We drove out to a public airfield in Houston to do our first test flight. Our pilot (Warren) put the plane into full thrust and we took off from the ground in a distance of less than 15 feet! We had a smooth takeoff for about 3 seconds in the air and then our plane flipped upside down and crashed. From a video I took, we determined that our left and right wing aileron controls were flipped (classic mistake), which caused our plane to destabilize very quickly. Luckily, our plane suffered minimal damage with only our nose cone and tail taking damage. We decided against competing because we did not have enough time left in the semester to make fixes and run more test flights before we all left for summer jobs across the country.
Engineering Design Showcase:
Our team presented our autonomous drone in the Rice Engineering Design Showcase to compete for prizes against other undergraduate engineering teams.Our team won the 2023 Best Underclassman Design Project Award for a $1000 cash prize, beating all student design teams at Rice University with no senior members.